Внедрение комплексной системы автоматизации на предприятиях ИГ УПЭК: обзор проекта, организация работ, методология внедрения
В.Б. Ковалевский, П.В. Стрелков (Pro|TECHNOLOGIES) , Э.А. Симсон (ИГ УПЭК)
Предисловие
Инновации… Возможно, это слово скоро будет вызывать только негативные ассоциации. В лучшем случае, усмешку. Мы постоянно слышим про модернизацию экономики, техническое перевооружение, инновационные технопарки… Идеи, конечно, правильные и красивые, но где результаты? Этой статьей мы, специалисты компании Pro|TECHNOLOGIES, хотим открыть цикл публикаций, посвященных опыту успешной (в плане конкретных результатов, а не только идей) реализации проектов коренной реорганизации конструкторско-технологической подготовки производства (КТПП) промышленных предприятий.
Точка отсчета
Индустриальная группа “Украинская промышленно-энергетическая компания” (ИГ УПЭК) является одной из крупнейших частных компаний Украины, специализирующихся в машиностроительном бизнесе. Компания была основана в 1995 году, а сегодня на её предприятиях работает порядка 7000 человек. ИГ УПЭК производит комплектующие, узлы и оборудование для железнодорожной, автомобильной, сельскохозяйственной, машиностроительной и металлургической отраслей.
Подразделения ИГ объединены в четыре дивизиона:
- железнодорожный – поставляет комплектующие для производства и обслуживания тягового и подвижного состава на предприятия и железные дороги СНГ;
- автодивизион – сотрудничает с ведущими конвейерными предприятиями, производящими автомобильную, сельскохозяйственную и дорожно-строительную технику;
- электротехнический – поставляет асинхронные электродвигатели, электронасосы общего и специального исполнения (в том числе, скважинные насосы), а также кормоизмельчители для животноводческих хозяйств;
- станкостроительный – производит вальцешлифовальное и круглошлифовальное оборудование для металлургии и других отраслей промышленности.
В состав ИГ УПЭК входят предприятия следующей специализации:
- Харьковский подшипниковый завод – подшипники для железнодорожного транспорта, авто- и сельхозмашиностроения;
- Лозовской кузнечно-механический завод – мосты для тракторной и дорожно-строительной техники, узлы, детали, полуфабрикаты для железнодорожного транспорта и автомобильной отрасли;
- Харьковский электротехнический завод – электродвигатели для промышленного и бытового оборудования, бытовые и промышленные насосы;
- Украинская литейная компания – литые изделия и полуфабрикаты для железнодорожного транспорта, авто- и сельхозмашиностроения;
- Харьковский станкостроительный завод ХАРВЕРСТ– станки для машиностроения, металлургии, подшипниковой отрасли;
- УПЭК-Техсервис – предоставление предприятиям ИГ УПЭК технических услуг (модернизация станков, профилактическое ТО оборудования, плановые ремонты, устранение аварийных ситуаций);
- Инженерный центр УКТБ ПП – ведущий центр разработки инновационных продуктов, таких как роликовые и шариковые подшипники для железнодорожного и автомобильного транспорта и других отраслей;
- Инженерный центр УКБ ТШ – разработка сельскохозяйственных машин и орудий для земледелия, элементов трансмиссий и шасси для строительной техники, автомобилей и тракторов;
- Инженерный центр СКБ – разработка электромашин, насосов и агрегатных устройств;
- Инженерный центр ОКБШС – разработка оборудования для обработки валков металлургических прокатных станов, шлифовки коленчатых и распределительных валов автотракторных двигателей, деталей трансмиссии автомобилей, деталей, подшипников и т.д.
На официальном языке всё это звучит весьма внушительно. А если неофициально… С чего же всё начиналось? Вспоминаю один из первых приездов в КБ завода ХАРВЕРСТ… Было это в декабре2008 г. Взгляду предстало типичное КБ советских времен. Ряды кульманов, ворохи бумаги, исчерканные чертежи, по которым даже старожилы струдом могут понять, что именно актуально в настоящий момент, умирающее технологическое оборудование и выпускаемая продукция отнюдь “непервой свежести”. Всё это типично, я видел такое много раз. Но меня поразили люди: опытнейшие специалисты, средний возраст – под 60, а в глазах – надежда. Надежда на новое, лучшее. На то,что завод, которому были отданы многие годы, будет расти, развиваться, не перейдет на копирование третьесортного ширпотреба, а станет выпускать современную продукцию, изделия своей разработки! Наверное, именно в этот момент и появилась уверенность, что наш проект просто не может быть неуспешным. С такими специалистами, совместными усилиями можно свернуть горы. В дальнейшем эта уверенность подтвердилась.
“Мы приняли принципиальное решение реализовывать этот проект, несмотря на разворачивающийся в Украине и во всём мире промышленный и финансовый кризис. С одной стороны, это отражает уверенность в успешном преодолении трудностей. С другой стороны, новая угроза – это одновременно новая возможность! Мы намерены осуществить не только переоснащение значительной части технологического оборудования, но и полное перевооружение ИТР и, таким образом, встретить будущий промышленный подъем принципиально другой компанией”.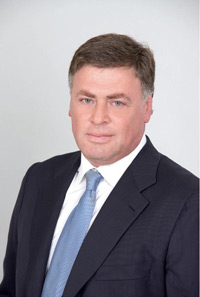
А.М. Гиршфельд, президент УПЭК
Итак, в начале работы мы, с одной стороны, имели типичную (попросту говоря – “нулевую”) ситуацию в аспекте информационных технологий в КТПП, а с другой – коллектив, который был на 100% готов к изменениям, к повышению эффективности своей работы (причем, это относится не только к какому-то одному, а ко всем заводам УПЭК, и, конечно же, центральному офису).
К чему мы должны были прийти
Немаловажно отметить, что в этот период (конец 2008 – 2009 г.) в мире разворачивался экономический кризис. Как писал журнал “Forbes”, если в кризис люди кладут зубы на полку,
значит выгодно производить полочки для зубов… Ничего личного – это бизнес, надо ловить момент. Но есть и другой подход. Кризис – лучшее время для модернизации производства, процессов разработки изделий, всей компании в целом. Почему? Потому, что кризис, безусловно, закончится, и к этому моменту надо быть на гребне технологической волны. Собственники компании УПЭК захотели использовать время экономического кризиса в том числе и для того, чтобы осуществить коренные изменения в конструкторско-технологической подготовке производства и вывести предприятия индустриальной группы на мировой уровень.
Таким образом, целями проекта стали:
- Сокращение сроков КТПП не менее, чем в два раза;
- Сокращение затрат на КТПП не менее, чем на 25%;
- Повышение технического качества изделий;
- Снижение материалоемкости;
- Повышение эффективности планирования и управления;
- Сохранение накопленного опыта.
Руководство УПЭК определило, что для достижения поставленных целей должны быть решены многие задачи (рис. 1).
Далее мы будем вести речь только о задачах в области ИТ, изменения инженерных процессов и, частично, технического перевооружения. Выделим из них самые важные:
- изменить процессы конструкторской и технологической подготовки производства на базе современных технологий;
- автоматизировать всю инженерную деятельность индустриальной группы – конструкторскую, расчетную, технологическую, производственную (станки с ЧПУ) и управленческую (!) на базе единой программной платформы;
- уйти от бумажного документооборота во внутрикорпоративном управлении и в инженерной деятельности;
- создать единую среду управления инженерными разработками, связывающую все конструкторские бюро (КБ), инженерные центры (ИЦ), заводы, управляющую компанию (включая все их подразделения);
- создать электронные архивы всей конструкторской, технологической и другой инженерной документации, а также базы знаний и систему управления данными по каждому проекту;
- интегрировать создаваемую комплексную систему автоматизации (КСА) с другими программными платформами (в частности ERP) и пакетами, применение которых обусловлено спецификой предприятий.
Вот такие масштабные задачи были поставлены.
Не менее впечатляли и организационные аспекты проекта: полем деятельности становились пять территориально удаленных предприятий с разным типом производства (от крупносерийного до единичного) и конструкторских бюро, плюс центральный офис. Количество потенциальных пользователей новой системы – более 400.
И еще одно требует упоминания: целевая установка по срокам. Собственники хотели провести коренные преобразования предприятий в минимально возможное время. Проект должен быть реализован за один, максимум полтора года!
Эх, дороги… Дорожная карта проекта
Итак, цели поставлены, масштабы определены, перечень задач обозначен. Следующий логичный шаг – выбор программной платформы и компании,которая будет осуществлять внедрение. Здесь необходимо проведение тендера, однако в этой статье мы пропустим данный этап. Согласитесь, победителю (как вы наверняка уже догадались, им стала компания Pro|TECHNOLOGIES) нескромно расписывать в красках, как он обогнал всех конкурентов. Пусть о проведении тендера рассказывает сам заказчик. Со своей стороны, хочу лишь отметить, что в нём участвовали практически все известные поставщики САПР/PDM (PTC, Dassault Syst?mes, Siemens PLM Software) и компании, осуществляющие внедрение их продуктов.
Готовность номер один, ключ на старт…
Мы начнем наш обзор сразу с подготовительного этапа проекта. Считаю, этот этап является одним из самых важных. Именно в процессе подготовки работ завязываются отношения между людьми, участвующими в проекте. Именно на этом этапе создается план работ – та самая дорожная карта, которая в результате должна привести к успеху. Именно на этом этапе, как мне кажется, мы, совместно с заказчиком, заложили прочный фундамент, который в дальнейшем помог реализовать этот проект, невзирая на все трудности. Среди основных “кирпичиков” в этом фундаменте я бы выделил:
Режим стратегического партнерства УПЭК – Pro|TECHNOLOGIES – PTC
Под этой красивой фразой скрывается очень простая истина. Счастья (в данном случае мы говорим об успехе внедрения) нельзя достичь в одностороннем приказном порядке – только совместными усилиями заказчика и внедренца, и никак иначе. Ответственность лежит и на той, и на другой стороне. Односторонние усилия к результату никогда не приведут. И хотя это вроде бы простая вещь, лежащая на поверхности, но договориться об этом “на берегу”, до начала активной фазы проекта, бывает ох как непросто. А еще сложнее соблюдать эту договоренность в ходе работ.
“Мы больше не хотим строить заводы и линии по производству стружки. Наша задача – создать инженерную компанию с приоритетной ставкой на нематериальные активы: инженерные решения, специальные знания, программные продукты”.
А.М. Гиршфельд, президент УПЭК (цитата из выступления на совещании по стратегии УПЭК, май 2008 г.)Нам это удалось, и в результате появилась продуманная и взвешенная организационная структура проекта (рис. 2)
Проектами такого масштаба нельзя управлять в одиночку, это просто нереально. Для этого проекта нам была необходима команда, которая охватывала бы несколько уровней управления. Первый уровень – это стратегическое управление работами со стороны собственников и высшего руководства заказчика и нашей компании. Второй уровень – директора проекта со стороны заказчика и со стороны Pro|TECHNOLOGIES. В их руках сосредоточено тактическое и оперативное управление ходом работ: планирование и контроль исполнения планов, принятие наиболее ответственных технических решений, управление ресурсами проекта.
Следующий организационный элемент – команда экспертов по отдельным направлениям (САПР, расчетные системы, электронный архив, обучение, бизнес-процессы, ИТ), которая подчиняется непосредственно директору проекта. Задача экспертов – вникать во все тонкости происходящего по соответствующему направлению работ, осуществлять координацию этих работ со всеми остальными участниками проекта. Всё это – управление на уровне центрального офиса индустриальной группы.
За управление работами внедрения непосредственно на заводах отвечают заместители генеральных директоров по комплексной системе автоматизации. Это специальная должность, которая была введена в каждом подразделении (юридическом лице), участвующем в проекте. Уровень этой должности высокий – второе лицо на предприятии. С экспертами взаимодействуют так называемые ключевые пользователи предприятий. Это наиболее квалифицированные и инициативные сотрудники КБ и заводов, непосредственно работающие в тех подразделениях, которые затрагивает внедрение. Такой ключевой пользователь должен быть в каждом подразделении, в “минутной доступности” для остальных пользователей системы из своего отдела.
Выстроив такую цепочку, мы смогли обеспечить управляемость процессом внедрения на всех уровнях – от высшего руководства до рядового конструктора и технолога.
Еще одним важнейшим аспектом стало то, что анализ получившейся организационной структуры проекта позволил выявить реальный недостаток в управленческих ресурсах на стороне заказчика. В результате заказчик пошел на то, чтобы нанять дополнительных сотрудников для участия в проекте. Это – одна из интересных особенностей проекта. Очень мало компаний, готовых пойти на дополнительный набор персонала именно под проект внедрения. В итоге эта стратегия себя полностью оправдала.
Понимание и принятие заказчиком нашей методологии внедрения
Методология… Сколько всего об этом уже было сказано и написано. Столько, что многие уже воспринимают методологию внедрения как маркетинговый ход, а не реальное руководство к действию. Мы с этим категорически не согласны. Наша методология – живой документ, свод правил и принци пов, который постоянно пополняется в соответствии с приобретаемым опытом. Каждый проект привносит в методологию что-то новое, полезное, позволяет нам развиваться, двигаться вперед.
Донести до заказчика накопленный опыт по организации внедрения, детально объяснить нюансы этого процесса, которые мы хорошо понимаем – вот одна из задач подготовительного этапа. С другой стороны, заказчик, прекрасно зная специфику своих процессов и своей работы, конечно же, вносит определенные корректировки в наши подходы. В итоге заказчик и внедренец должны иметь одинаковый взгляд на то, как выстроить процесс внедрения, какие организационные приемы применять, как формировать этапы работ, как организовать взаимодействие. Если не договориться по этим вопросам в самом начале, то дальше будет много проблем со взаимодействием. В решении этой задачи – согласовании применяемой методологии внедрения – нам помогли большой опыт, наличие формализованных документов, описывающих нашу методологию внедрения, реальные примеры реализации других проектов. Практическим результатом этой работы явилась согласованная с заказчиком “дорожная карта” внедрения (рис. 3), концептуально отображающая последовательность основных этапов проекта.
Рис. 3. “Дорожная карта” проекта
Детальное календарное планирование
“Тщательно спланированный проект всегда стремится в два раза превысить сроки и в три раза – бюджет. Плохо спланированный, как правило, не завершается никогда”. Что тут можно добавить… Мы спланировали свой проект очень тщательно, поэтому получили гораздо лучшие результаты. В самом начале работ мы детально расписали, что будет происходить в ближайший год: кто, что и когда будет делать в нашем проекте. Получился календарный план, состоящий из 1025 задач. Мало кто верил в ценность этого документа, и, тем более, в то, что написанное будет в точности исполнено. Как оказалось – зря. По завершению проекта мы имели превышение сроков менее чем на 25%, а бюджета – менее чем на 5%. Профессионалы оценят эти цифры: для таких масштабных проектов внедрения это исключительно хорошие результаты. И во многом это достигнуто именно благодаря тщательности планирования, детальной и выверенной постановке задач.
Технический проект
Следующий важнейший шаг – определение того, как должно выглядеть законченное решение. Еще до начала каких бы то ни было работ по настройке системы, обучению пользователей, отработке практических примеров обе стороны – и внедренец и заказчик – должны четко понять, какой будет система после завершения всех проектных работ. Иными словами, надо сделать “чертеж” системы, или, как мы это называем, Технический проект. В этом вопросе можно провести очень простую аналогию. Никто в здравом уме и твердой памяти не рискнет изготавливать в железе какое-либо машиностроительное изделие без конструкторской документации. Сегодня информационные системы зачастую превосходят по сложности изделия машиностроения. Соответственно, мы просто не имеем права начать “производство”, до того как будет готов “чертеж” системы. Именно эта задача и решается на этапе анализа и реорганизации бизнес-процессов.
Почему не просто анализ, а еще и реорганизация? Всё просто:без изменения бизнес-процессов не будет никаких инноваций, а будет просто автоматизация того, что есть. Да, автоматизировав процессы “как есть”, мы тоже получим прирост производительности, повысим качество изделий, сократим сроки. Но это будет прирост, повышение, сокращение на единицы или доли процентов. А кому интересны такие несерьезные показатели при таких расходах на внедрение (думаю, ни для кого не секрет, что бюджет комплексного внедрения КСА может составлять цифру с шестью нулями, причем в USD). Если по результатам проекта мы весело отрапортуем, что повысили производительность труда конструкторов, например, на 1.7%, то, в лучшем случае, вызовем смех у любого современного руководителя. Серьезные показатели можно получить только после серьезных изменений!
Откуда эти изменения могут появиться? А вот это вопрос непростой… Достаточно распространен такой подход: сейчас у вас задачи выполняются последовательно, давайте сделаем их параллельными! Конечно, такие изменения имеют право на существование. Однако, если этим всё и ограничивается, то говорить о каких-либо инновациях не приходится.
Для нас важнейшим источником информации об изменениях, которые мы можем предложить нашим заказчикам, служат так называемые “лучшие практики” (best practices) зарубежных компаний. Откуда мы берем эту информацию? Дело в том, что PTC, в отличие от многих конкурентов, не просто разрабатывает и продает программное обеспечение. В структуру компании PTC входит подразделение Global Service Organization, отвечающее за консалтинг. Это подразделение работало со многими крупнейшими мировыми компаниями во многих отраслях и, естественно, накопило богатейший опыт в области организации процессов КТПП. Этот опыт в формализованном виде и представляет собой те “лучшие практики”, которые мы можем предложить нашим заказчикам – это уже настоящие инновации. Использование процедур и методик, которые применяются ведущими мировыми компаниями для разработки своих изделий – чем не благодатная почва для оптимизации и изменения собственных процессов?!
Так ломать или строить? Ответ на этот вопрос, как и в обычной жизни, в каждом случае будет индивидуален. Иногда проще снести дом и построить на его месте новый, чем делать капитальный ремонт. А иногда можно обойтись только косметическими правками. Важно найти правильное соотношение для каждого конкретного проекта. В нашем случае было очевидно, что измененные процессы будут работать только тогда, когда они основаны на том лучшем, что сложилось на предприятиях ИГ УПЭК в ходе развития. С другой стороны, нам необходимо было включить в существующие процессы “лучшие практики”, причем только те, которые реально могут применяться на конкретных предприятиях (по самым разным причинам). Именно поэтому фундаментом для строительства новых, инновационных процессов стал анализ той системы организации работ, которая сложилась на предприятиях ИГ УПЭК – то есть, анализ процессов “как есть”.
Анализ “как есть” – это не просто описание, формализация существующих бизнес-процессов, но и выявление “узких мест”, согласование с заказчиком способов их устранения. Зачастую специалисты и руководители предприятий сами прекрасно понимают, в каких местах процесс неэффективен, и отлично представляют, как улучшить положение дел. Но, по разным причинам (заедает текучка, “инициатива наказуема” и пр.), самостоятельно устранить эти проблемы им не удается.
Итак, можно сказать, что самыми важными моментами при подготовке технического проекта являются:
- наличие “лучших практик”;
- строительство, а не разрушение – необходимо опираться на существующие процессы предприятия;
- выявление и устранение “узких мест” на основе мнения профессионалов в соответствующей предметной области.
Второй аспект разработки технического проекта – уточнение приоритетов автоматизации и реорганизации, учитывая, что бюджет проекта не резиновый. Необходимо четко, на уровне технических деталей, определить, что входит в рамки проекта, а какие вопросы останутся за бортом (это, кстати, предмет для дальнейшего обсуждения и следующих проектов).
В результате, еще до начала масштабных работ по развертыванию системы, заказчик видит четкую и ясную картину – как будут работать предприятия после завершения работ по внедрению. Именно на этом этапе мы с заказчиком получили по-настоящему единую команду, которая говорит на одном языке. Были “притерты” все наиболее критичные моменты, касающиеся будущей организации процессов, а руководство и специалисты заказчика были ознакомлены с основами внедряемых систем.
Что нам стоит дом построить…
Подготовительный этап пройден, технический проект системы разработан. После этого и мы, и специалисты УПЭК уже четко представляли последовательность всех дальнейших шагов. Остальное, как говорится, дело техники. В соответствии с “дорожной картой” основными техническими этапами внедрения являлись:
- Внедрение САПР Pro/ENGINEER;
- Создание электронного архива и библиотек на базе Windchill;
- Автоматизация технологической подготовки производства с помощью САПР ТП ВЕРТИКАЛЬ и Windchill MPMLink;
- Постановка проектного управления в среде Windchill ProjectLink;
- Интеграция PLM-решения с ERP.
Реализация каждого из этих этапов была выстроена по одинаковой, логичной и простой схеме (рис. 4).
Немного поговорим о каждой группе задач:
Разработка технической спецификации
Если технический проект – это своеобразный чертеж КСА, то техническая спецификация – это технологическая документация для создания каждого из элементов решения. В этом документе мы описываем все настройки, которые должны быть выполнены для того, чтобы система полностью отвечала требованиям заказчика – тем требованиям, которые утверждены в техническом проекте.
Обучение группы внедрения
Речь идет об обучении тех ключевых пользователей, которые были выделены еще на этапе формирования организационной структуры проекта. Именно они, как бойцы первой линии, должны будут тестировать разработанное решение и оценивать, насколько настройки системы соответствуют реальным потребностям предприятия – уже не в теории, а на практике. Соответственно, ключевые пользователи должны обладать всей полнотой знаний о системе, знать все тонкости и технические особенности функционала. Именно поэтому обучение этих специалистов проводится на самых ранних стадиях.
Настройка, подготовка инструкций
На данном этапе выполняются технические настройки системы, которые были определены в технической спецификации. Кроме этого, разрабатываются детальнейшие инструкции для конечных пользователей по работе с полностью настроенной системой. Эта задача уникальна для каждого предприятия, как уникальны его бизнес-процессы и, соответственно, настройки КСА. Результатом является комплект пользовательской документации, которая максимально полно описывает систему, адаптированную под конкретного заказчика.
Тестирование
Конечно же, в идеале всё должно работать с первого раза, без сучка и задоринки. Как же может быть иначе?! К сожалению, в жизни так не бывает, поэтому этап тестирования необходим. Прежде чем обучать конечных пользователей, передавать решение в эксплуатацию, необходимо всё проверить и перепроверить все семь раз. В том числе: сами настройки, инструкции для пользователей (насколько они полны, понятны и корректны), и, конечно же, бизнес-процессы, которые заложены в систему. Это – последний шанс внести какие-либо изменения.
Передача в промышленную эксплуатацию
После того как решение протестировано, необходимо устранить все выявленные замечания и, совместно с заказчиком, принять решение о том, передаем ли мы разработанную систему в эксплуатацию. Если решение положительное (а иного и быть не может после выполнения всех описанных выше шагов), проводится обучение конечных пользователей (в нашем случае – это более 400 человек) и система вводится в эксплуатацию приказом по предприятиям.
Вот и всё, можно двигаться дальше и реализовывать по аналогичной схеме следующий этап, в соответствии с планом работ.
Результаты
Итак, к чему мы это всё… Мы начали разговор с того, что этот проект, являясь по-настоящему инновационным, принес УПЭК реальные измеримые результаты. Так что же это за результаты? Некоторые из показателей, подтвержденных заказчиком, приведены на рис. 5.
Но это далеко не всё, есть и другие критерии и показатели. Вот как оценивает руководство УПЭК результаты по отдельным проектам, выполненным с использованием КСА:
- сроки КТПП сократились более чем в два раза. Выпуск чертежей на нормализованные элементы стал занимать минуты, разработка технологических процессов на основе аналогов – несколько часов, оформление технологических карт – несколько минут;
- затраты на КТПП сократились более чем на 25% за счет ускорения процесса разработки. К примеру, в результате автоматизации создания РОТК (рабочих операционных технологических карт) высвободились технологи, которые ранее формировали их вручную;
- повысилось техническое качество изделий, поскольку, за счет предварительного 3D-проектирования, на 80% сократился брак, связанный с ошибками на стадии разработки, фактически исчезли ошибки собираемости изделий;
- с помощью прочностных расчетов удалось повысить прочностные и эксплуатационные характеристики изделий, добиться снижения их материалоемкости;
- повысилась эффективность планирования и управления. Система мониторинга Windchill дает возможность руководителю любого уровня – от директора предприятия до линейного руководителя – контролировать ход выполнения процесса или проекта, получая в любой момент полную информацию о состоянии работ по любому изделию или его части;
- внедрена система проектного управления. Введение единой методологии управления проектами снижает риски, что, в свою очередь, приводит к уменьшению стоимости проекта и увеличению прибыли предприятия. Windchill позволяет оперативно получать общую картину по всем проектам организации для принятия оперативных решений. Windchill дает возможность планировать, контролировать и динамически распределять ресурсы, задействованные в проектах, перебрасывать их на критически важные проекты;
- накопленный опыт стал фиксироваться. Вся документация сохраняется в едином электронном архиве и в дальнейшем используется как база для новых инженерных разработок, чем достигается оптимальность конструктивных и технологических решений.
Вот такие результаты! Кроме того, хотелось бы отметить, что проект внедрения КСА на предприятиях ИГ УПЭК обладает целым рядом уникальных особенностей. И всё это вполне реально и для вашего предприятия, если рассматривать проект создания комплексной системы автоматизации не как способ автоматизировать то, что есть, а как инновационный проект, проект по радикальному повышению эффективности конструкторско-технологической подготовки производства.
“Это один из крупнейших проектов в Восточной Европе. По своим масштабам, комплексности и срокам реализации он не имеет аналогов ни в Украине, ни в России”.
А.В. Волков, генеральный директор Pro|TECHNOLOGIESПосле подписания акта сдачи-приемки (слева направо: А.В. Чудновец, первый вице-президент УПЭК; П.В. Стрелков, директор по корпоративным проектам Pro|TECHNOLOGIES; В.Б. Любецкая, директор проекта внедрения, УПЭК; Э.А. Симсон, директор УПЭК по R&D и IT; А.В. Волков, генеральный директор Pro|TECHNOLOGIES)
Вместо заключения, или Продолжение следует
Надеюсь, вам, уважаемые читатели, была интересна эта статья. В течение года мы планируем подготовить серию публикаций по отдельным аспектам этого по-настоящему уникального проекта.
В числе запланированных тем – обсуждение вопросов, касающихся особенностей внедрения программных продуктов, которые составляют комплексную систему автоматизации (Pro/ENGINEER, Windchill PDMLink, Windchill MPMLink, ВЕРТИКАЛЬ). Отдельные статьи планируется посвятить технологической подготовке производства, разработке постпроцессоров для станков с ЧПУ и интеграции Windchill с системой 1С (используется на предприятиях индустриальной группы как система управления производством). Более подробно мы познакомим вас с организацией процесса обучения и сертификации специалистов, взаимодействию с университетами региона в рамках проекта.
Возможно, по прочтении этого материала у вас появится желание выяснить какие-то дополнительные, специфичные для этого (и не только для этого) проекта вопросы. Мы с радостью готовы пообщаться с вами и поделиться нашим опытом.
Обращайтесь, и мы не оставим ваши вопросы без ответа!
Планируемый цикл статей, посвященных проекту
Авторы:
Ковалевский Владимир Борисович – технический директор компании Pro|TECHNOLOGIES;
Стрелков Павел Васильевич – директор по корпоративным проектам компании Pro|TECHNOLOGIES;
Симсон Эдуард Альфредович – директор ИГУПЭК по R&D и IT, д.т.н., проф., лауреат Госпремии Украины, заслуженный деятель науки и техники Украины.